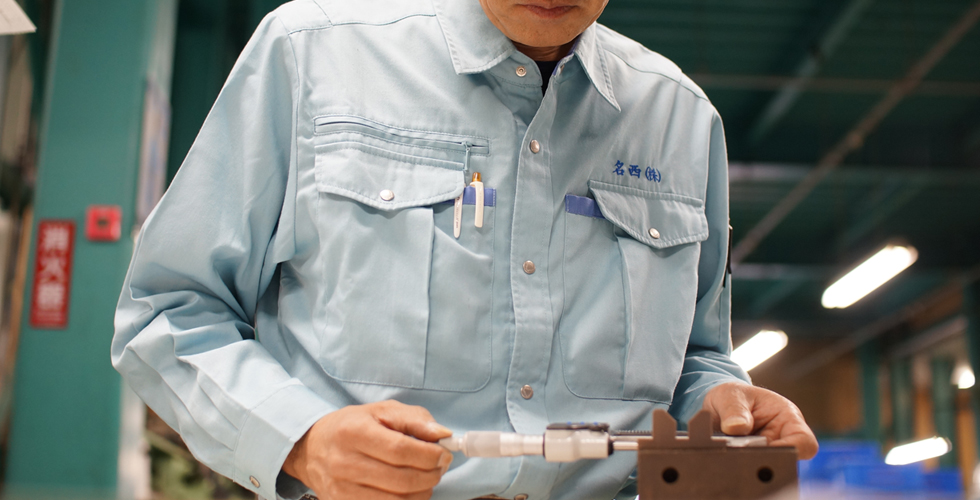
あらゆる樹脂の可能性を
知り尽くしたモノづくり企業
「名西」が生み出す付加価値
VA・VE提案
VA提案とは、既存の製品のコスト削減や、
長寿命化・軽量化・生産工程の簡略化・事故防止など
大幅な付加価値向上を伴う品質改善を実現させる提案の事をいいます。
また、名西株式会社のVA提案の特色として、
壊れた既存製品の修理によるトータルコストの削減や環境への取り組みの支援も強みとしています。
名西株式会社では、50余年に渡り培った高度な技術と知見を以て、長期的・複眼的に分析し、現在使用している製品が、お客さまにとってさらに良いものになりますようにご提案をさせていただきます。
VE提案とは、0から製作をする提案をさせていただく事を指します。
開発設計からおこない、機能・品質や、コスト削減等、
お客さまの想像を超えた付加価値提案をさせて頂きます。
名西株式会社には、開発・設計段階から様々な形で設計変更や工法転換などのVA・VE実績が多数あります。
あらゆる樹脂の可能性をとことんまで知り尽くした名西株式会社ならではご提案をさせていただきます。
また、現状で樹脂部品をご利用の企業様で、
強度や耐久性などの問題で、新しい素材への置き換えをご検討の場合でも、
樹脂切削加工で様々な素材の試作品を短納期で作成することが可能ですので、
是非ご相談ください。
VA事例既存製品の改善
強度を変えずに驚異的な軽量化とコスト削減・短納期の実現事例
- 軽量化
- コスト削減
- 短納期化
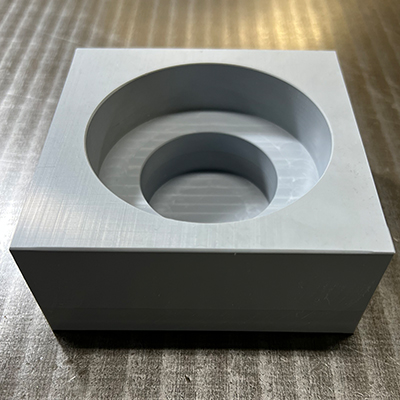
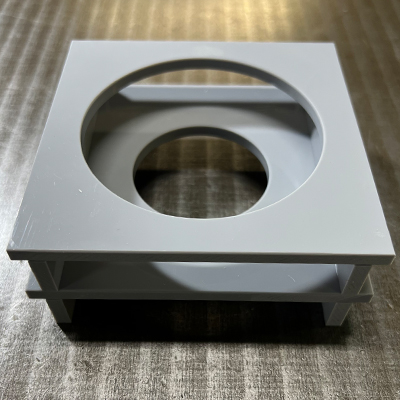
中空化する事で、強度を変えずに70%もの軽量化を実現する事とともに、製造時間も70%短縮する事を実現できました。また、この事によりコストも50%以上の削減を実現できました。
ビスの落下・錆による設備への事故防止
- 事故防止化
- 軽量化
- 短納期化
- コスト削減化
- 製品寿命向上
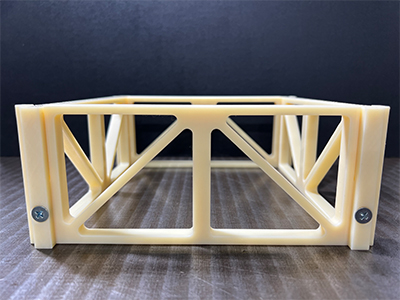
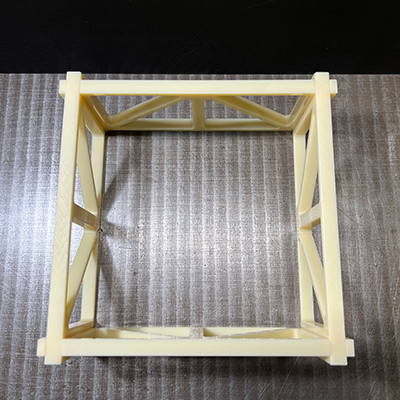
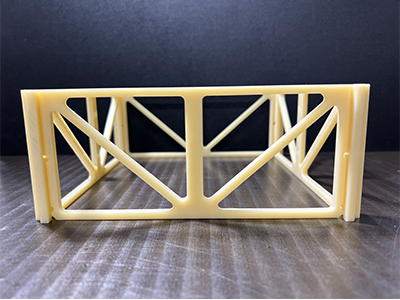
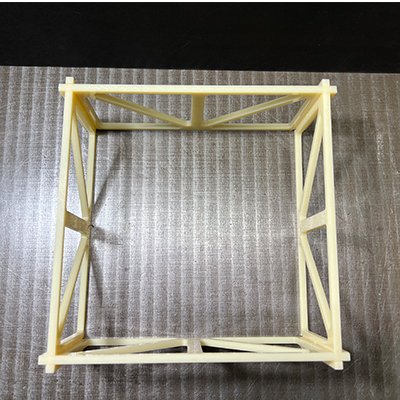
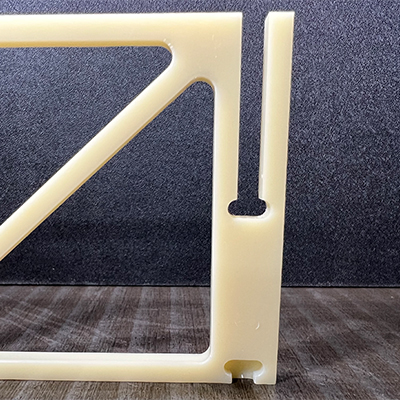
高度な切削技術によるはめ込み構造への変更により、ビス止め構造の事故リスクをなくし、錆による製品劣化の防止を実現。また、同時に50%以上の軽量化も実現。組付け時間も30%以上短縮を実現する事ができました。
7種類の大型受けを1種類の大型受けへ共通化
- 共通化
- 工程削減
- コスト削減
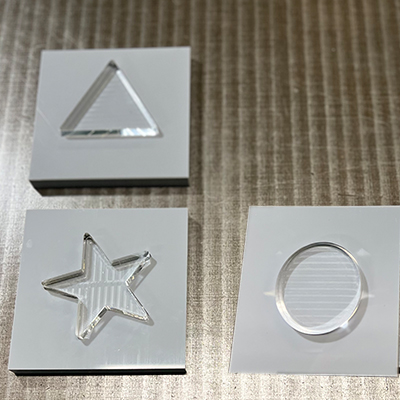

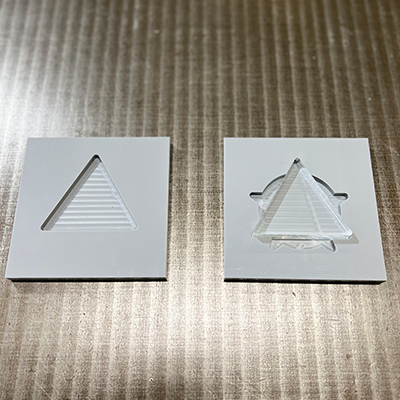
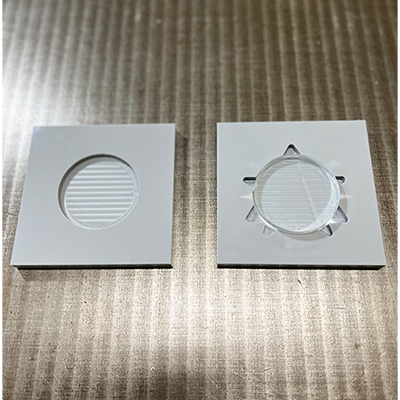
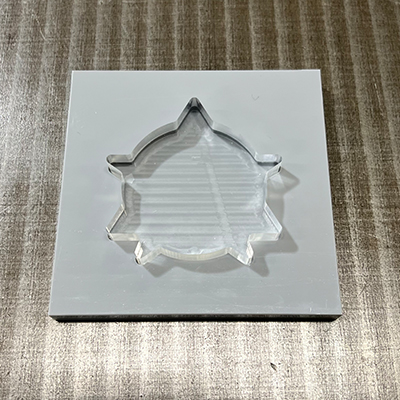
「受けの共通化」を実現する事により、従来は7種類の「大型受け」を1種類の「大型受け」にする事ができ、保管場所の80%削減・工程時間の80%削減、それに伴う30%以上のコスト削減も実現する事ができ ました。
VA事例工具管理の改善
工具管理の簡素化事例
- 作業時間の短縮化と効率化
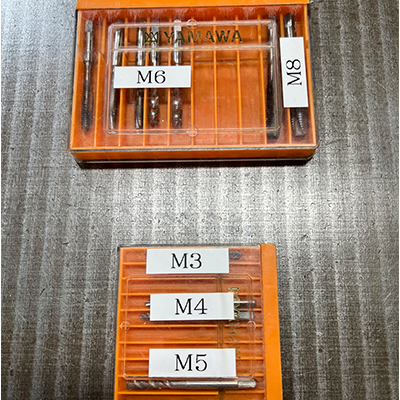
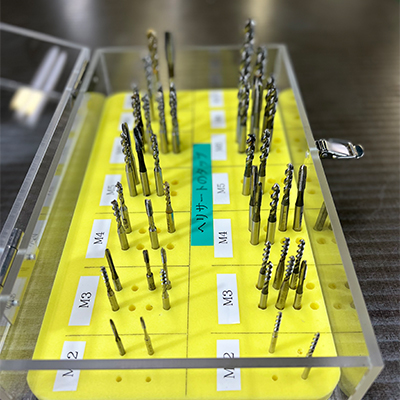
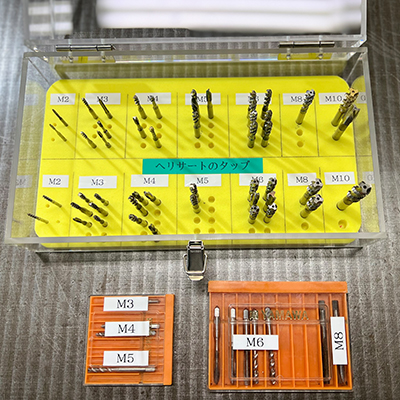
工具管理のトレイを開発する事で、工具管理に係る時間ロスを20%以上削減できました。定位置化を徹底する事ができるようになる事で、探す手間・間違いを撲滅する事も出来ました。
VA事例既存製品の修理
破損製品の修理対応事例
- 短納期
- コスト削減
- 廃棄削減
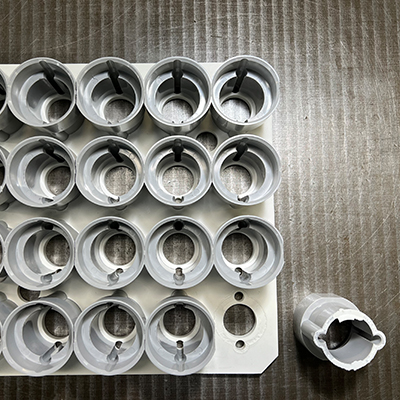
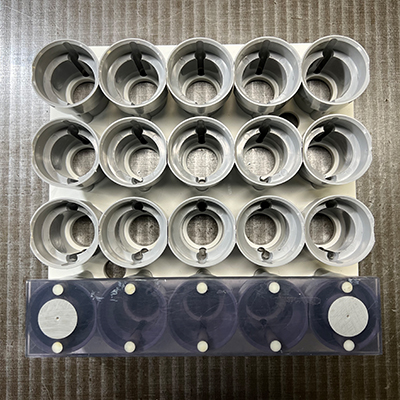
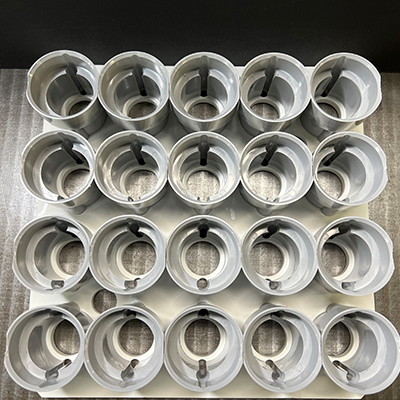
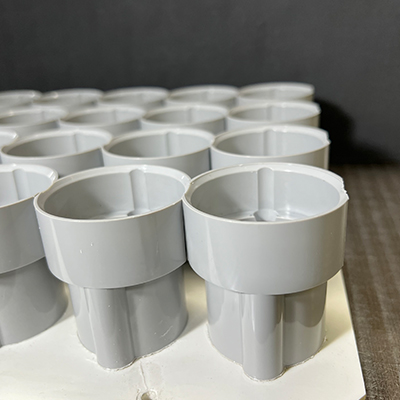
従来は、破損製品は廃棄し、やむなく新規製作を依頼していましたが、名西では高度な修理技術を用い、復元できるものは修理対応をします。この事例では、新規製作に比べ、70%以上のコスト削減、納期に至っては、10分の1となりました。それだけでなく、廃棄による環境へのダメージにも配慮するという企業責任も果たす事ができました。
VE事例用途別特注部品製作事例
製品に傷のつかない「樹脂製スクレーパー」の開発
- シール剥離工程における製品傷の改善
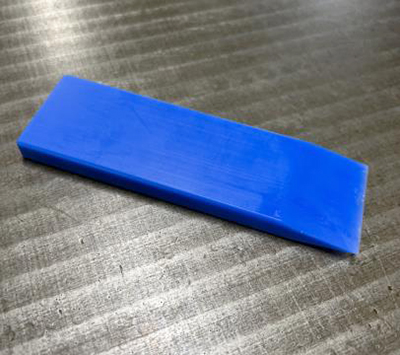
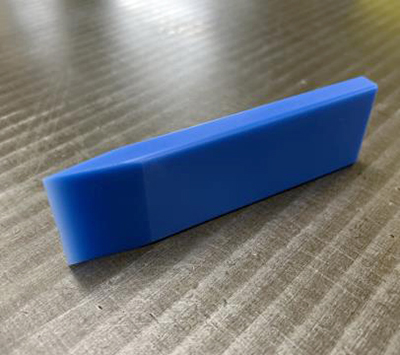
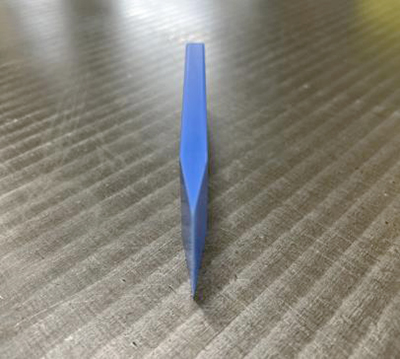
お客様より、製造工程の中の「シール剥離工程」において、金属製スクレーパーを使用してシール剥離を行っていたのですが、その際に強く擦ると製品に傷が入ってしまうとの相談を受け、樹脂製のスクレーパーに替えてみてはどうかと提案しました。
その後、お客様の製品の材質とシール剥離の強度を踏まえ、特注の樹脂製スクレーパーを開発。製品に傷が殆どつかず、シール剥離も金属製スクレーパーの時より格段に楽になったとのお喜びの声を頂き、その後幾度も追加注文を頂いています。
ナット部に傷のつかない「樹脂製スパナ・六角レンチ」の開発
- ナット部の締め工程における傷の改善
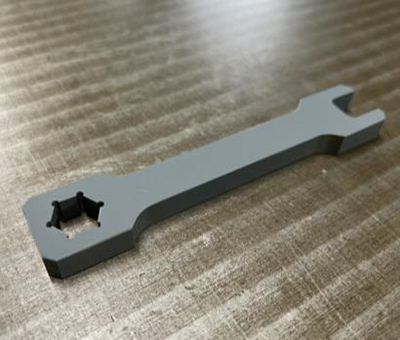
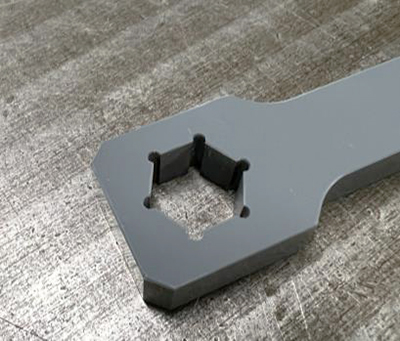
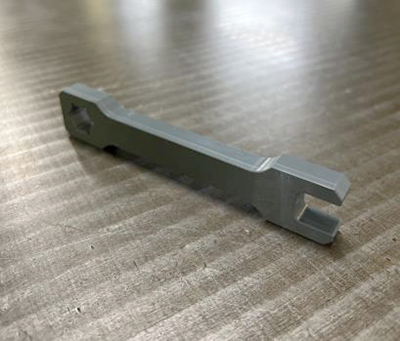
お客様より「ナット部の締め工程において、市販の金属製スパナ及び六角レンチスクレーパーを使用してナット部の締めを行っているが、その際に強く締めるとナット部に傷が入ってしまう」との相談を受け、樹脂製の特注スパナ及び六角レンチに替えてみてはどうかと提案しました。
その後、特注の樹脂製スパナ・六角レンチを開発。強く締めてもナット部に傷がつかず、又、樹脂製のため軽く、作業効率も高まったとのお喜びの声を頂きました。
VE事例(試作品製作事例)
成型品(量産品)の型取りも可能な高精度な試作品製作事例
- 3Dプリンターでは実現不可能な「寸法精度が極めて高い」試作品
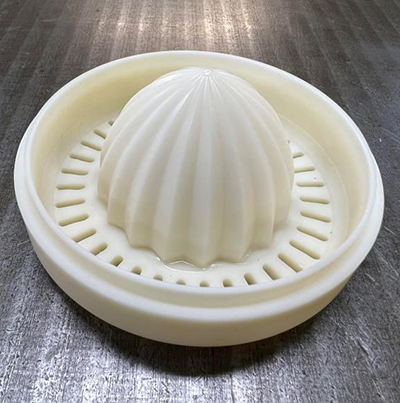
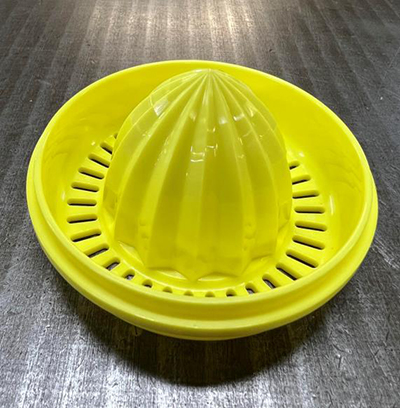
どのような製品であっても、必ず製作をするのが試作品(プロトタイプ)です。名西では、企画段階から関わらせて頂き、プロトタイプ製作において、構造上問題の無い軽量化やコスト削減提案なども同時に実施し、付加価値の高い製品づくりに貢献してまいります。
3Dプリンターでは製作不可能な、寸法公差精度の極めて高い試作品を製作しますので、そのまま量産品の型取りが可能です。
VA事例既存製品の改善
強度を変えずに50 %以上の軽量化と、油抜きにより品質向上及び着脱工程の大幅時短を実現
- 軽量化・品質向上(油抜き)・作業効率改善
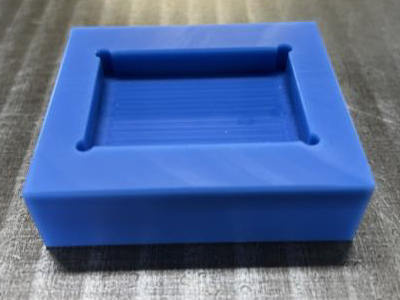
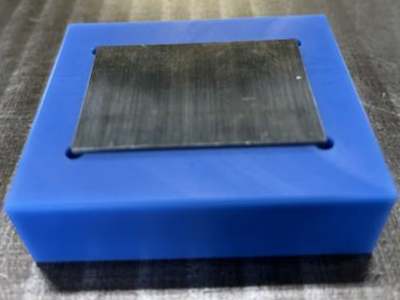
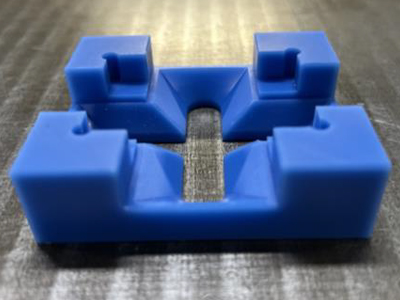
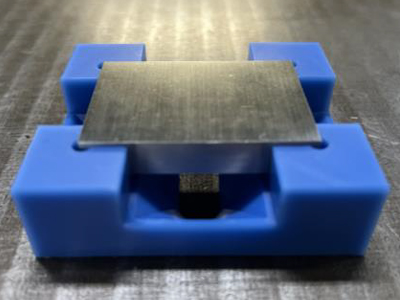
お客様の工場内では、製品の油抜きと着脱工程の問題解決のためのワーク受けの改善取り組みはあったものの、ワーク受けに大幅なソリが生じてしまい、寸法精度が下がるために断念していましたが、名西の高精度なソリ制御技術により、寸法精度を維持したままで、お客様の理想を実現する事が出来ました。
VA事例既存製品課題の改善
反りを制御 × 寸法公差100分台を実現
- 単品切削加工対応にて、反り制御と寸法公差の改善
外部からの解決提案としては、金型を作り、成形品として量産するしかないとの事で、我が社に相談に来られました。
反りを制御 × 100分台の寸法公差の実現
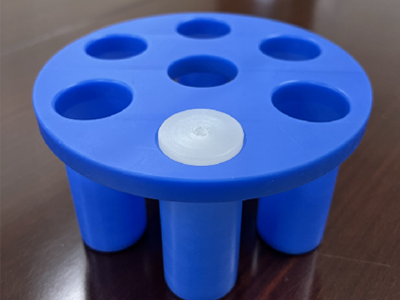
車用のアルミホイール洗浄の際、ナット部の傷防止のためのカバーです。量産品ではなく、これまでは反りがどうしても出てしまい、伴い寸法が大きく公差外してしまう問題を抱えていました。金型を作らなければならないかと悩まれていましたが、その場合は多大なコストが発生し、量産しなければ採算が合わない中、名西にご相談を頂きました。名西では、従来の切削加工における「材質内の収縮差」による反りが出てしまう原因を考慮し、収縮差の原因である「残留応力」のバランスを取る、独自の高精度切削技術を用い、結果として、単品切削加工において、反りを制御し、寸法公差100分台を実現する事ができました。